Planification de la production typique
Comment évaluez-vous la qualité et faisabilité de la planification de la production? Les opérations se déroulent toujours telles que planifiées? Il n’y a aucune perte de temps non anticipée? Si ce n’est pas toujours le cas, alors la simulation des opérations est un outil à utiliser durant la planification de la production. Cela permet d’ordonnancer les activités de manière à réduire au minimum les pertes de temps et autres attentes improductives, tout en allouant suffisamment de temps pour amortir la variation des procédés.
Le cycle hebdomadaire typique de la production, par exemple dans une usine agroalimentaire, est : obtenir la liste des ordres de production, planification et exécution de la production. Les ordres de production varient d’une semaine à l’autre, donc la planification doit être revue à chaque semaine.
Lors de la planification, la complexité de l’exercice découle des nombreuses combinaisons et contraintes à considérer, par exemple : produits différents, emballages différents, caractéristiques des équipements, compatibilités produit-produit et produit-équipement, séquences et tailles de lots, etc. Lors de l’exécution, la difficulté de l’exercice découle des réalités du plancher de production : fiabilité des équipements, délais de changement de produit, attentes diverses, variabilité naturelle dans les débits et temps de cycle, etc.
À a fin de la semaine : catastrophe, le plan ne s’est pas déroulé comme prévu! On a dû effectuer du temps supplémentaire, des commandes ont été livrées en retard aux clients, les équipes de production remettent la faute à la planification irréaliste reçue, et les équipes de planification remettent la faute à l’efficacité des opérations qui a été en-deçà des espérances… Et s’il était possible de planifier en anticipant comment les opérations vont se dérouler?
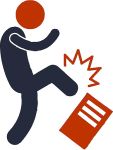
Simuler pour mieux planifier
Il est possible de capturer le savoir-faire des spécialistes en opérations afin d’anticiper comment une cédule de production sera exécutée. Une technique possible repose sur la simulation par événements discrets. C’est une approche permettant de modéliser les flux de matières (pièces, matières en vrac, débits), tâches à exécuter, cédules de production et règles de décision. De tels modèles permettent de bien comprendre les interactions entre les éléments d’un système de production et d’en estimer la productivité. L’utilisation de nombres aléatoires est l’ingrédient clé : cela permet de mimer la variabilité des processus, et donc, d’évaluer les risques d’erreur et la précision des prédictions.
La préparation d’un modèle de simulation par événements discrets, lorsque faite selon les règles de l’art, oblige d’impliquer les gens du plancher de production : ce sont les opérateurs qui sont les mieux à même de fournir les détails et subtilités à modéliser. De plus, la variabilité dans les performances réelles et les efficacités observées historiquement sont prises en considération. Donc, ce type modèle est littéralement le plancher de production représenté dans un ordinateur, en format pratique et rapide. C'est un jumeau numérique! Il est possible de tester de nombreux scénarios afin de trouver les plus favorables… tels que la cédule de production réaliste et optimale!
Minimiser les pertes de temps avec une simulation
De retour avec la tâche de planification hebdomadaire : maintenant qu’il est possible d’anticiper la réponse de la production pour une cédule donnée, les planificateurs peuvent maintenant ajuster les séquences, tailles de lots et assignations aux équipements de manière à :
- Réduire les temps d’attente
- Réduire le nombre de changement de produits
- Insérer les maintenances et inspections aux moments opportuns
- Équilibrer adéquatement la charge de travail entre les équipements
- S’assurer de terminer les lots à temps pour les clients
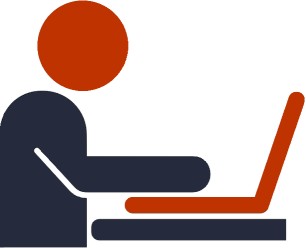
Puisque les estimations des durées de production sont obtenues en considérant les nombreuses contraintes d’opération ainsi que les diverses sources de variation et perturbation, la probabilité que le plan hebdomadaire soit exécuté tel que prévu est grandement augmentée.
Et il y a quelques effets secondaires à l’utilisation de telles simulations : la durée de l’exercice de planification est réduite et implique moins de personnes, les méthodes de planifications sont automatiquement standardisées, il est plus facile de transférer le savoir-faire à d’autres ressources, le climat de travail est amélioré, et ainsi de suite.
Combien coûte la préparation d’une simulation? Combien coûtent les pertes de temps et leurs conséquences?
Illustration avec une usine de produits laitiers
Une usine de pasteurisation et emballage de produits laitiers peu avoir à gérer plus de 100 formulations et plus de 50 formats d’emballage, soit plus de 200 produits différents à ordonnancer à chaque semaine. Certains de ces produits ont des colorations, saveurs, acidité et durée de vie incompatibles, voire même allergènes. Le cadre normatif en vigueur impose des fréquences de nettoyage et stérilisation. Environ le 2/3 de la production doit être faite vers la fin de chaque semaine pour répondre aux habitudes de consommation. Quel casse-tête!
Un modèle a été développé à l’aide du logiciel de simulation Flexsim. Ce modèle considère des éléments tels que : modes et débits de pasteurisation, une intelligence quasi-artificielle pour l’assignation des réservoirs de stockage, les taux de remplissage et efficacités de chaque remplisseuse en fonction de chaque produit et chaque format d’emballage, et les règles régissant les nettoyages et stérilisation. Le modèle interprète la cédule de production et s’assure que tous les lots sont exécutés à temps compte tenu des éléments mentionnés précédemment.
Les tableaux ci-dessous illustrent l’utilité de la simulation. On évalue le pourcentage de lots prévus terminés à temps pour chaque remplisseuse à chaque jour de la semaine. Une cédule produite « normalement » a été évaluée par simulation (tableau de gauche). Les opérateurs savent que, pour les jeudis et vendredis (jours 5 et 6), les cédules sont généralement irréalisables. Le tableau de gauche brosse exactement ce portrait. Après environ une heure de travail avec la simulation, un planificateur a produit une cédule dont la performance apparaît sur le tableau de droite. Sans l’outil de simulation, le même exercice aurait nécessité 5 à 6 heures pour une petite équipe ne disposant pas de la puissance de calcul du simulateur.
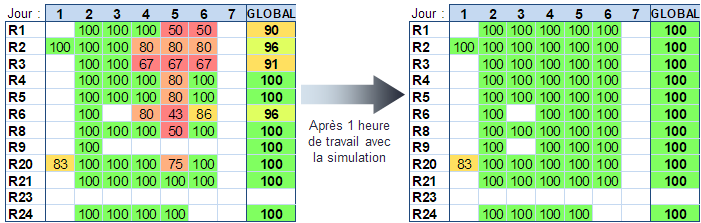
Cette nouvelle cédule est-elle crédible? Les opérateurs qui l’ont exécutée ont rapporté très peu de déviations et tous les lots ont effectivement été produits à temps. La somme de toutes les heures d’attente de toutes les remplisseuses (manque de produit) s’élevait à 254 heures pour la cédule « normale », alors que pour la même charge de travail, la version améliorée de la cédule ne comportait que 60 heures d’attentes. Une réduction de 76% des pertes de temps! Et il ne s’agit que des pertes de temps d’opération, cela ne considère pas le temps économisé durant le processus de planification… Les planificateurs et gestionnaires disposent de plus de temps à consacrer à l’amélioration continue et à l’augmentation de la satisfaction des clients.
On pense pouvoir réduire les durées des nettoyages et stérilisations en modifiant les priorités d’allocation des équipements? Quelques vérifications par simulation confirment les meilleurs choix, et les essais durant la semaine de production confirment les impacts. Un cauchemar en planification survient lorsque de nouveaux produits sont mis en productions pour la première fois par l’équipe de marketing… Qu’à cela ne tienne, avec une telle simulation les impacts potentiels sont anticipés et amoindris avant qu’ils ne se présentent.
Un important volume promotionnel d’une grande bannière de supermarchés est demandé? La simulation a permis de répondre rapidement « oui, nous pouvons le faire » avec cédule réalisable à l’appui. Avec 194 heures disponibles pour produire au lieu d’attendre… Propriétaire d’un réseau d’usines voulant réduire les coûts de livraison en répartissant plus efficacement les volumes entre les usines? Environ cinq heures de travail de simulation ont été consacrés à trouver la nouvelle répartition plus économique!
En conclusion
En résumé, la planification hebdomadaire de la production est essentielle au fonctionnement d’une usine. Elle est efficace et réaliste seulement si les détails, complexités, contraintes et subtilités des opérations sont pris en considération. Pour ce faire, la simulation par événements discrets est une approche de modélisation tout indiquée. Les planificateurs disposant d’une telle simulation sont capables d’ajuster adéquatement les cédules de manière à réduire le stress opérationnel : moins d’imprévus, plus de marge de manoeuvre, charges de travail équilibrées, etc. Résultat : moins de pertes de temps, plus de temps de production.
De plus, dans un contexte visant à s’approcher d’un système de production Lean, la simulation est un outil permettant de réduire plusieurs gaspillages tant au niveau de la production que de la planification :
- Gaspillages de production : attente, déséquilibre de la charge de travail, délai de livraison, changements de produits inutiles, etc.
- Gaspillage de planification : erreurs et re-travail, surtraitement, frustration
Vous désirez en savoir plus?
Chez Différence, notre expertise est axée sur la statistique et la science des données, les applications du Lean et l'Excellence opérationnelle, ainsi que sur la simulation! Nous pouvons former, coacher et aider les praticiens à apprendre à utiliser la simulation. N'hésitez pas à demander plus d'information en nous contactant.
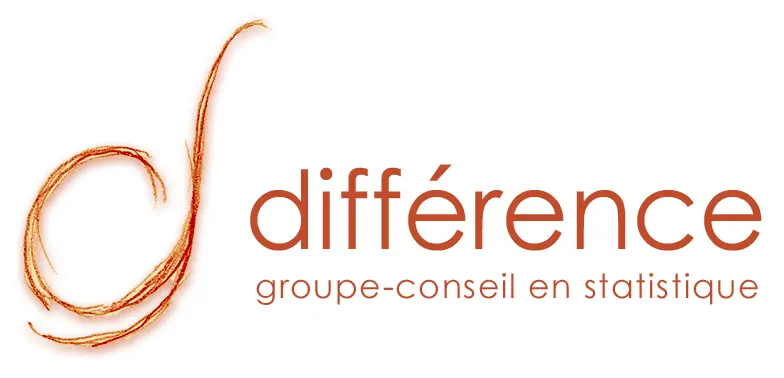